Kutaniyaki, a stunning Japanese ceramic from Ishikawa Prefecture, enchants with its five-color palette—red, yellow, green, purple, and blue—hand-painted on fine porcelain. Known as Kutani ware, each piece tells a story of nature and culture, gracing tables and collections globally. This guide dives into Kutaniyaki’s craftsmanship, unique styles, and modern charm, revealing why it’s a timeless gem for enthusiasts and collectors of Japanese porcelain.
1. What is Kutaniyaki?
Kutaniyaki, a distinctive Japanese chinaware from Kutani village in Ishikawa Prefecture, dazzles with hand-painted designs in five colors: red, yellow, green, purple, and blue. Part of Japan’s yakimono (pottery) tradition, “yaki” ties it to Kutani, highlighting its exquisite colored embellishments. Unlike other ceramics, Kutaniyaki’s vibrant artistry stands out, reflecting a 350-year legacy of evolving painting techniques.
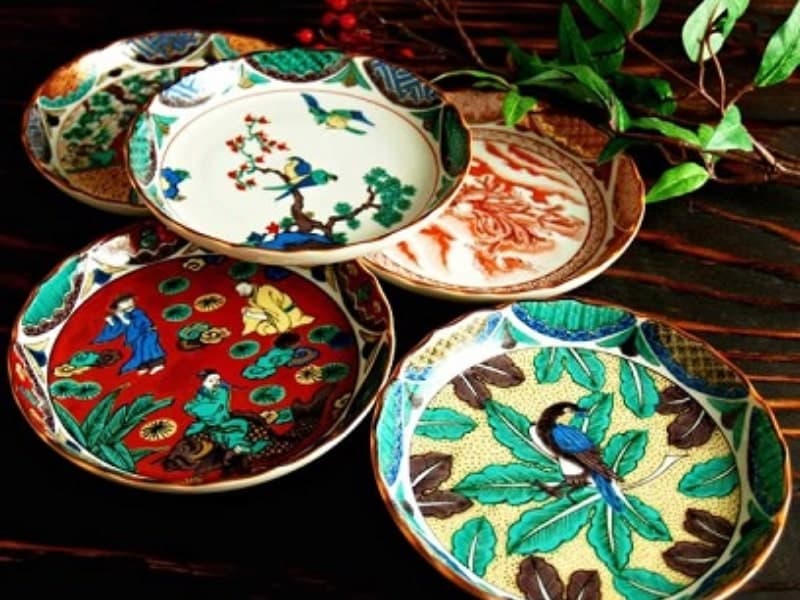
Known as Kutani ware, this Ishikawa craft blends tradition with modern flair, introducing bold, adorable designs into daily life. Its vivid colors and global appeal earn it the nickname “Japan Kutani,” attracting collectors and enthusiasts worldwide who cherish its timeless beauty and innovative charm.
2. The Origins Of Kutaniyaki: A Historical Journey
Kutaniyaki began with a first principle: ceramics unite utility and beauty. In 1655, Lord Maeda Toshiharu, ruler of Ishikawa Prefecture’s Daishoji Domain, tapped Kutani village’s porcelain stone to create a distinctive pottery. He sent artisan Goto Saijiro to Arita, Japan’s ceramic hub, to master techniques. The resulting Kutani kiln produced Ko-Kutani, early Kutani ware with bold designs inspired by Chinese and Kyoto ceramics. Unlike Arita’s delicate blue-and-white, Ko-Kutani’s vibrant aesthetic marked a unique artistic leap.
By the early 1700s, the kiln mysteriously closed, leaving Ko-Kutani as rare treasures. In the early 1800s, artisans like Aoki Mokubei revived Kutaniyaki, refining its bold style for modern times. Isolated in the Hokuriku region’s snowy terrain, Kutaniyaki flourished with vivid colors, as if defying winter’s gloom. This distinct vibrancy, rooted in its remote setting, set Kutani ware apart from ornate Imari or precise Arita, cementing its enduring place in Japanese porcelain history.
3. How Does Kutaniyaki Compare To Other Japanese Ceramics?
3.1 Kutaniyaki vs Arita and Imari
Kutaniyaki stands out among Japanese porcelain for its bold, multicolored designs, a stark contrast to Arita and Imari wares. While Arita pottery, often called Arita-yaki, emphasizes precision with delicate blue-and-white patterns, Kutaniyaki’s five-color palette—red, yellow, green, purple, and blue—bursts with painterly freedom, filling plates with vibrant landscapes or florals. Imari, an Arita offshoot, adds ornate gold and red accents for opulence, yet its structured motifs feel restrained compared to Kutani pottery’s expressive brushstrokes. This artistic liberty, rooted in Kutani’s Hokuriku heritage, makes Kutaniyaki a canvas of unrestrained beauty, unlike Arita’s meticulous elegance or Imari’s gilded formality.
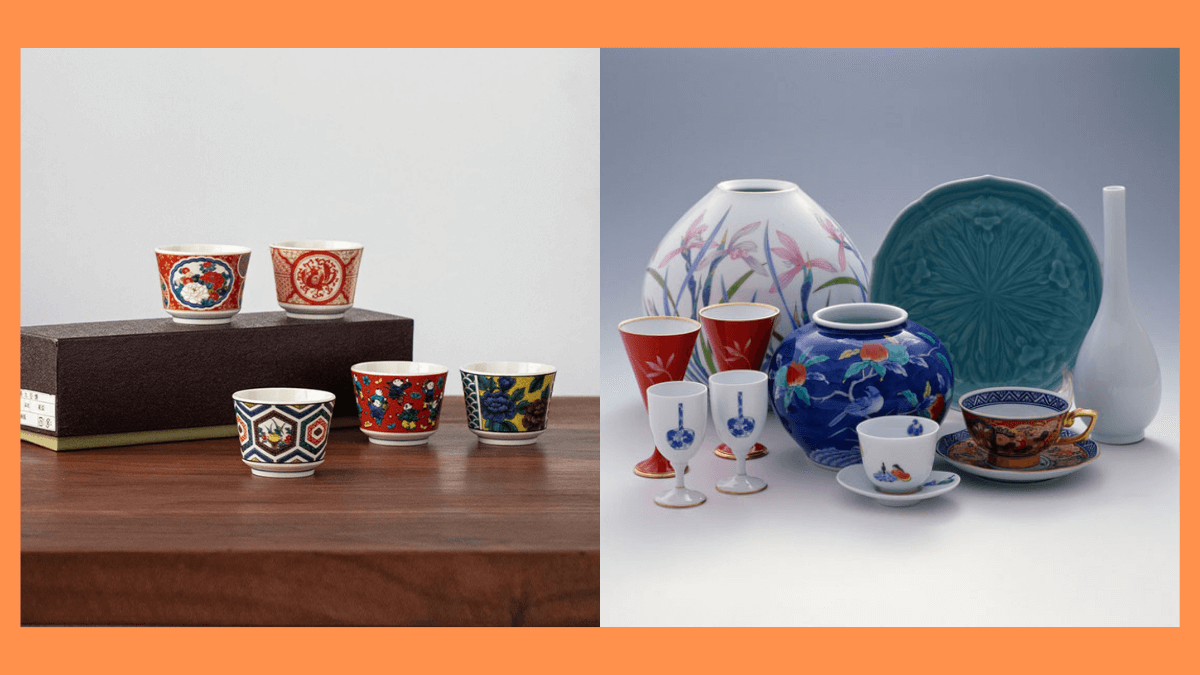
3.2 Kutaniyaki vs Bizen and Mashiko
Kutaniyaki’s polished porcelain also contrasts with Bizen and Mashiko’s rustic charm. Bizen-yaki, an earthy stoneware, embraces unglazed simplicity, its wood-fired textures ideal for daily meals. Mashiko-yaki, with its folk-art functionality, offers sturdy, handcrafted warmth. Yet Kutaniyaki’s glossy splendor elevates it to a luxury status, perfect for tea ceremonies or special occasions rather than everyday use. Picture a Kutani teacup glowing with peonies beside Bizen’s rugged bowl—each serves a purpose, but Kutani pottery’s vibrant finesse speaks to celebration, a unique ceremonial allure unmatched in Japan’s ceramic tapestry.
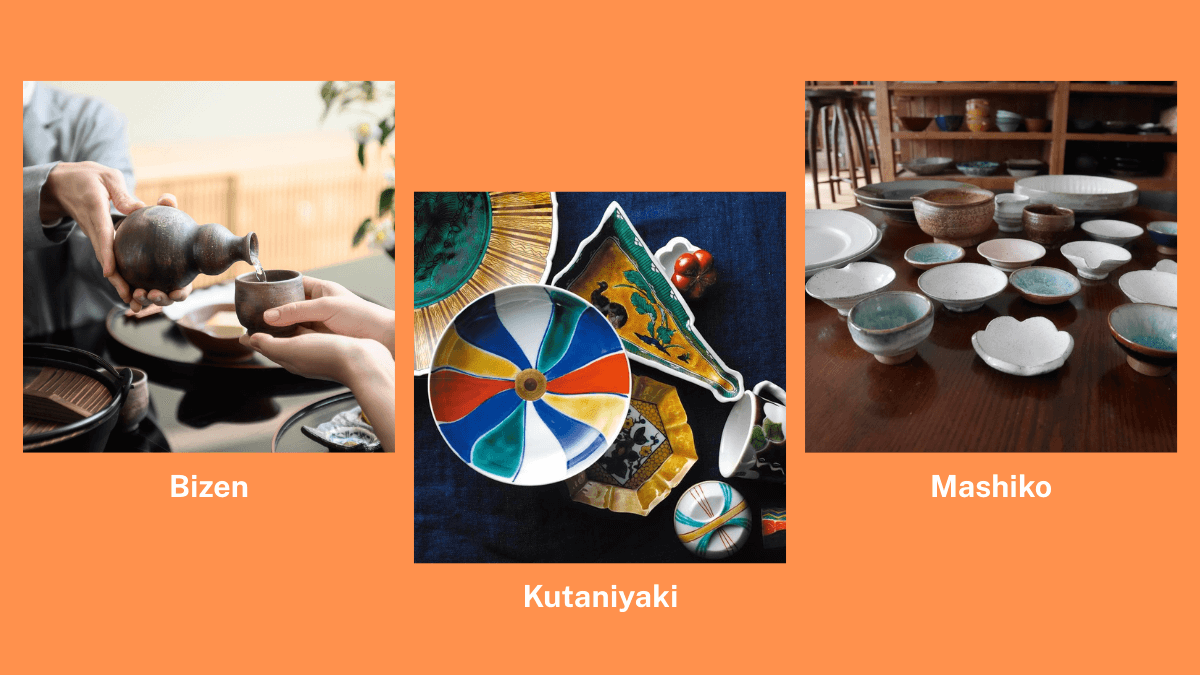
4. Special features of Kutaniyaki
Artisans begin with a white ceramic base, painting Komon patterns inspired by kimono designs using cobalt oxide-based zaffre for contours. The piece is fired in a kiln for seven hours, darkening the zaffre to define intricate lines. This initial firing hardens the base, preparing it for vibrant embellishments that distinguish Kutaniyaki’s artistry.
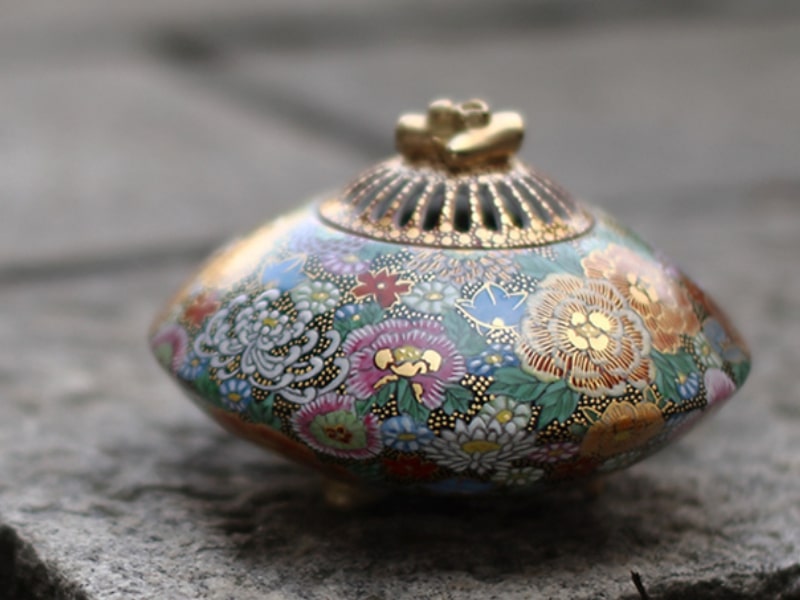
Next, the five Gosai-de colors—red, yellow, green, purple, and blue—are applied in thick strokes, creating a three-dimensional effect. The vessel is fired again at 800°C, transforming pigments into translucent hues via chemical reactions. The intricate Komon design gains depth as paint turns to glass, showcasing Kutaniyaki’s signature vivid and layered aesthetic.
>>> Read more: What are Japanese Tetsubin? Everything to Know About Cast Iron Kettles
5. How is Kutaniyaki Made?
Kutaniyaki’s creation transforms raw materials into vibrant porcelain through meticulous steps, blending artistry and precision. Artisans craft each piece with care, often requiring multiple firings and intricate painting to achieve its signature five-color brilliance. Here’s how Kutani pottery comes to life:
- Prepare the Clay: Pottery stone is mined, pulverized into powder, mixed with water, and strained to remove impurities. The clay is kneaded to eliminate air bubbles, rested, and shaped using a potter’s wheel (Rokuro-Seiki) or molds (Ikomi).
- Shape and Dry: Clay is coiled or pressed into forms like vases or plates, then trimmed for detail. Pieces dry in the sun and undergo biscuit firing at 800–900°C for eight hours, turning gray clay beige and strengthening it.
- Apply Glaze: A white Hakuyu glaze is evenly coated for a glass-like finish after firing. The piece is glost-fired at 1300°C for 15 hours, enhancing durability and preparing it for decoration.
- Paint and Decorate: Artisans sketch designs with pencil, then apply gosu (cobalt oxide) for blue outlines, which darken after firing. Noto gosu and wa-e no gu paints add the Gosai-de five colors—red, yellow, green, purple, blue. Overglaze is fired at 800–1000°C, fusing vibrant hues. Optional gold or silver leaf is added, fired again at 400°C for a luxurious touch.
This intricate process, rooted in Ishikawa’s tradition, crafts Kutaniyaki’s timeless beauty, captivating collectors worldwide.
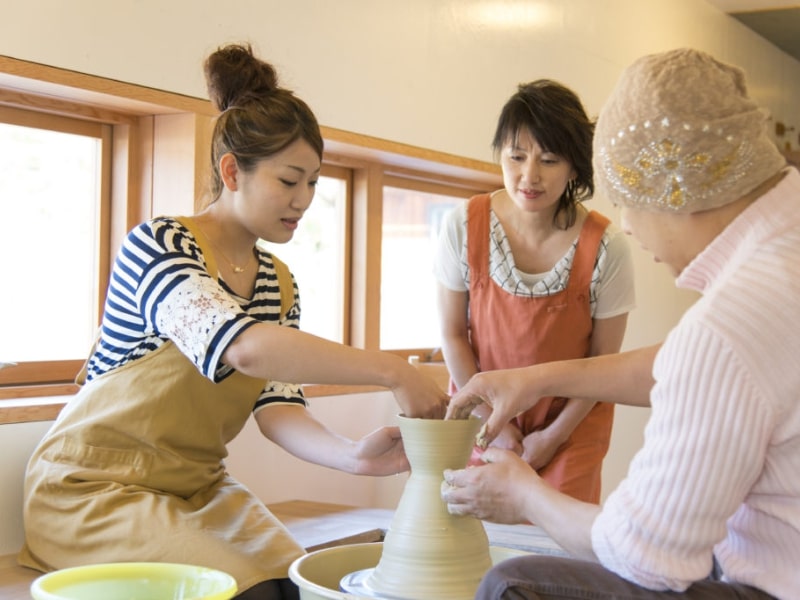
6. The typical styles of Kutaniyaki
6.1 Kokutani
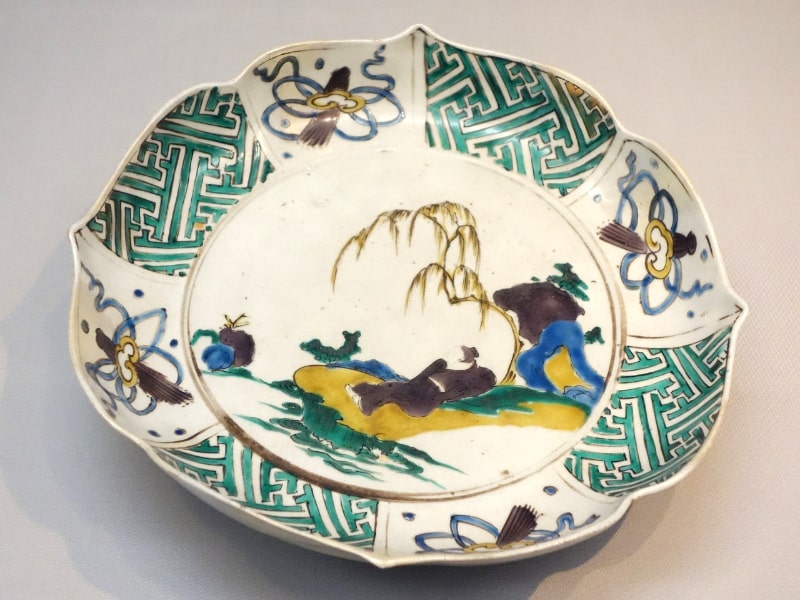
Toshiharu Maeda, a samurai from the Daishoji clan and captain of the Edo-era Ishikawa, gave the order to bake in this manner. Baked in the Kutani village, the design is semi-abstract and uses five hues Prussian blue, yellow, blue (green), red, and purple. It was influenced by the Kano style, painted with vivacious and free-flowing lines, distinguished by a striking design and excellent color palette.
6.2 Mokubei
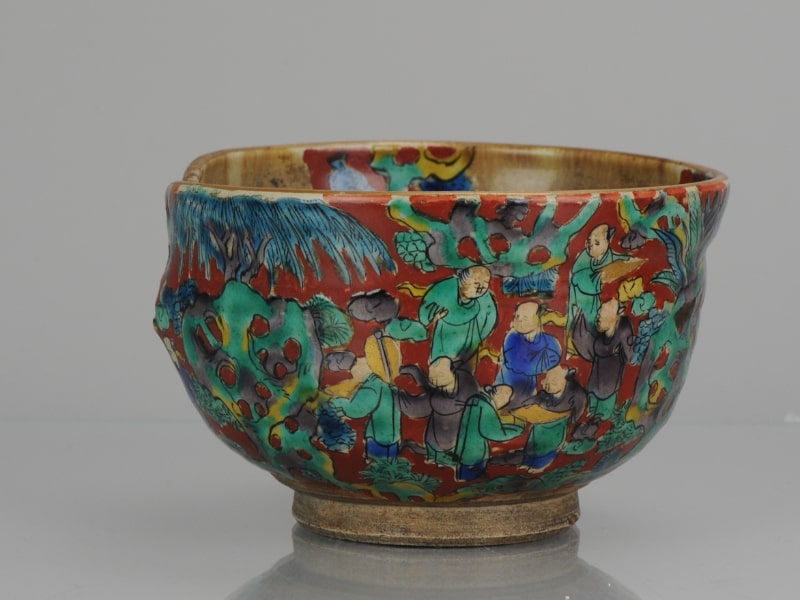
The Kasuga mountain kiln near Kanazawa, under the management of the Kaga clan, opens about 100 years after the Kutaniyaki waste kiln. A painting style in which Mokubei Aoki, a literatologist, was instructed to paint the front in red and uses five colors to show Chinese characters and other objects.
6.3 Yoshidaya
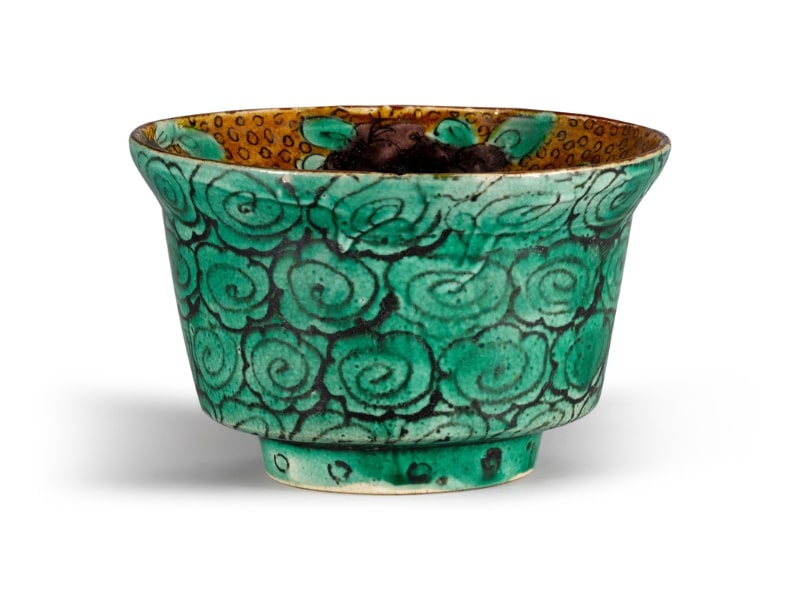
This design makes use of the Yoshidaya Denemon kiln with the intention of reviving Kutani. It is a style that was influenced by Aode Kutani’s paintings. The design primarily employs four hues – blue (green), yellow, purple, and iron blue – along with a variety of patterns and little patties to cover the entire surface and give it a solid appearance.
6.4 Iidaya
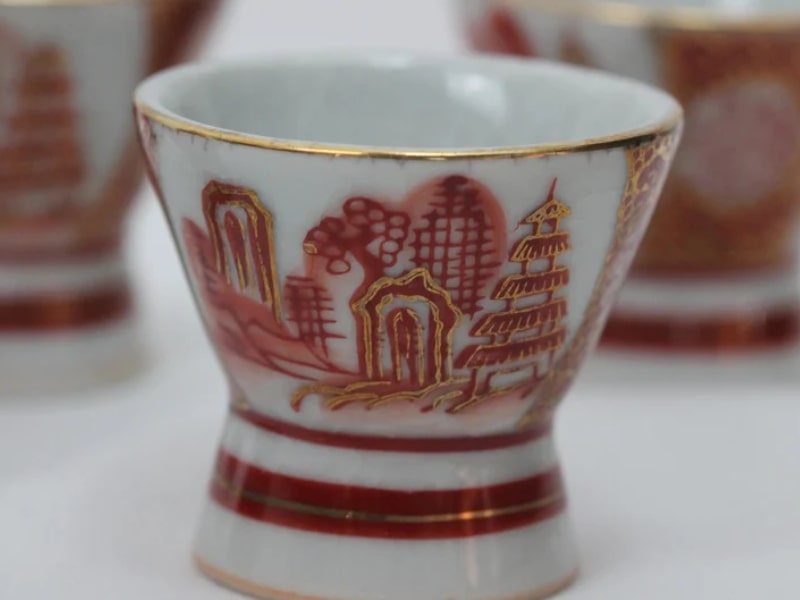
Baking in the Miyamotoya kiln, which replaced the Yoshida ya iron pod, is how this technique is accomplished. In red, it draws the viewer in while covering the entire diameter with tiny stamps. It also goes by the name Hachiro-shu after the principal worker, Iidaya Hachiro, who adds embellishments using the color gold.
6.5 Shouza
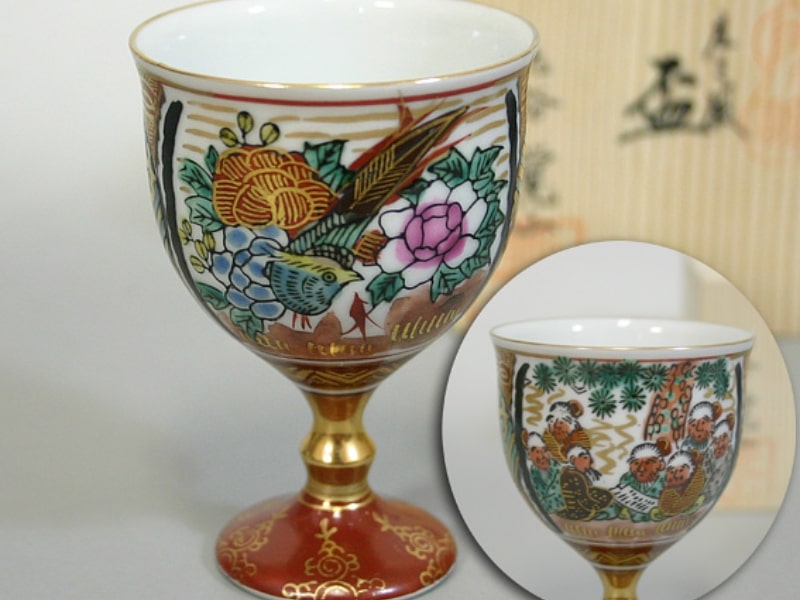
Shozo Kutani established the style of coloring in gold and combined all the techniques of Kokutani, Yoshidaya, Iidaya, Kanzaki, and others. This style, which is known as the “Japan Kutani,” became the predominant Kutani style after the Meiji era.
6.6 Eiraku
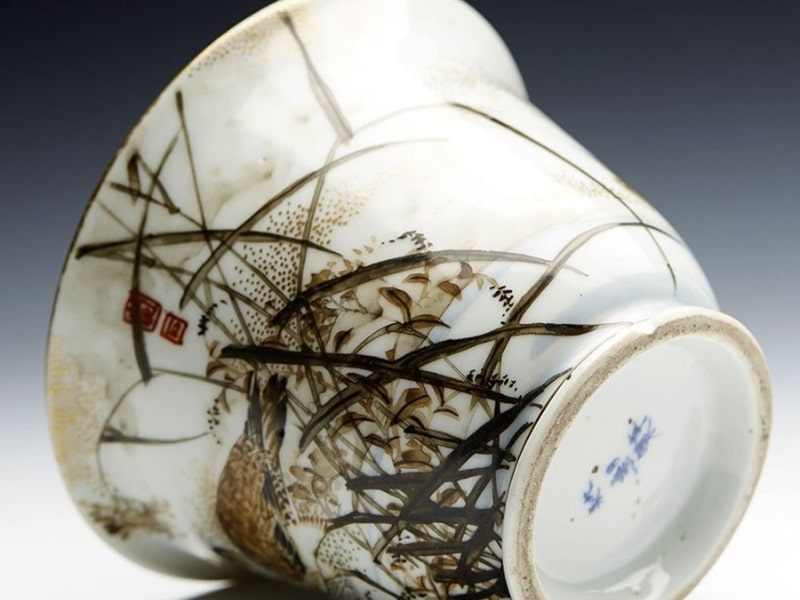
The Daisho clan of the Kaga clan branch first burned style in the Kutani major kiln. It is an opulent and elegant style of painting that uses only red and gold paint to cover the entire area.
>>> Read more: Japanese Kitchenware
7. Moritsuke & Kutaniyaki – The Inseparable Connection
The Japanese art of serving food is known as Moritsuke. While sets and basic dinnerware may be preferred in Western restaurants and homes, Japanese Moritsuke places more emphasis on the uniqueness of each piece. Making the meal appear presentable is the fundamental idea behind Moritsuke. This is accomplished through selecting the menu items and their seasonality, the dinnerware, and the way that everything is set up.

The hues and patterns of Kutaniyaki are perfect for setting a magical dinner table scene, even if the potters of Kutani may not intentionally think about Moritsuke when they create their pieces. You might serve pink sashimi with red Kutaniyaki or leafy greens with blue Kutaniyaki. Even after you’ve finished your meal, the table will still resemble a work of beauty because each Kutaniyaki bowl or plate is unique from the one before it.
8. Why is it important to preserve Kutaniyaki tradition?
The Ministry of Economy, Trade, and Industry formally recognized Kutaniyaki as a traditional craft in 1975. The next year, Ishikawa Prefecture officially recognized the craft as an Intangible Cultural Property.
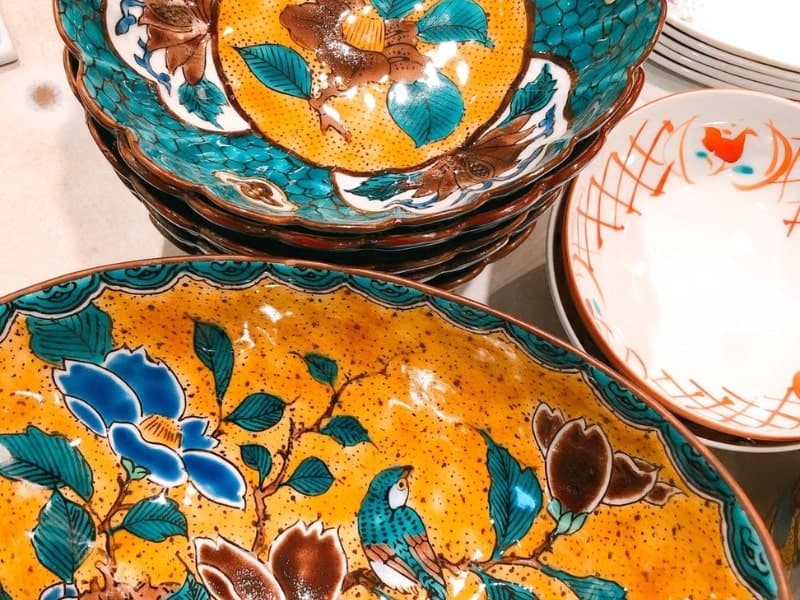
Kutaniyaki is a significant component of the Japanese ceramics industry with a lengthy and diverse history, but it has also established itself elsewhere. In fact, Japan gave Prince Charles of the United Kingdom a Kutaniyaki item on his wedding day. Many artisans now make Kutaniyaki with practical use in mind, whereas in the past much of it was used only for decoration. The art form is changing to fit the present while yet upholding the lovely tradition. Traditions should be preserved, especially if they fit into contemporary society.
9. Caring for Your Kutaniyaki
Kutaniyaki’s vibrant colors enhance meals, but proper care ensures longevity. Before first use, boil the pottery in water with a pinch of rice to coat it, reducing stains and odors. For sashimi, chill plates in ice water to prevent fishy smells from lingering. These simple steps keep your Kutani ware pristine.
After use, wash promptly with a soft sponge and mild detergent, avoiding dishwashers to protect gold or silver ornaments. Dry gently with a soft cloth, patting painted areas to avoid scratches. Never microwave pieces with metallic accents, as they can spark and damage the pottery, preserving your Kutaniyaki’s beauty for years.
10. Where to Find Authentic Kutaniyaki
10.1 Shopping in Japan
For those seeking authentic Kutani pottery, Japan offers unparalleled opportunities to discover handcrafted treasures. In Kanazawa, the Kutaniyaki Art Museum shop showcases a curated selection of vases, teacups, and plates, each reflecting Ishikawa’s rich ceramic heritage. Komatsu’s bustling markets, just near Kutani village, brim with local artisans’ works, offering everything from traditional to contemporary designs.
Don’t miss the annual Kutani Pottery Fair in Komatsu, where collectors and enthusiasts gather to explore vibrant five-color pieces directly from master craftsmen. Visiting these spots ensures you experience Kutaniyaki’s cultural depth while securing genuine items, often marked with kiln signatures for authenticity.
10.2 Online and Global Options
Can’t travel to Japan? Trusted online platforms bring authentic Kutaniyaki to your doorstep. Janbox connects you with Japanese retailers, offering a seamless way to buy Kutani pottery from marketplaces like Rakuten or Mercari.
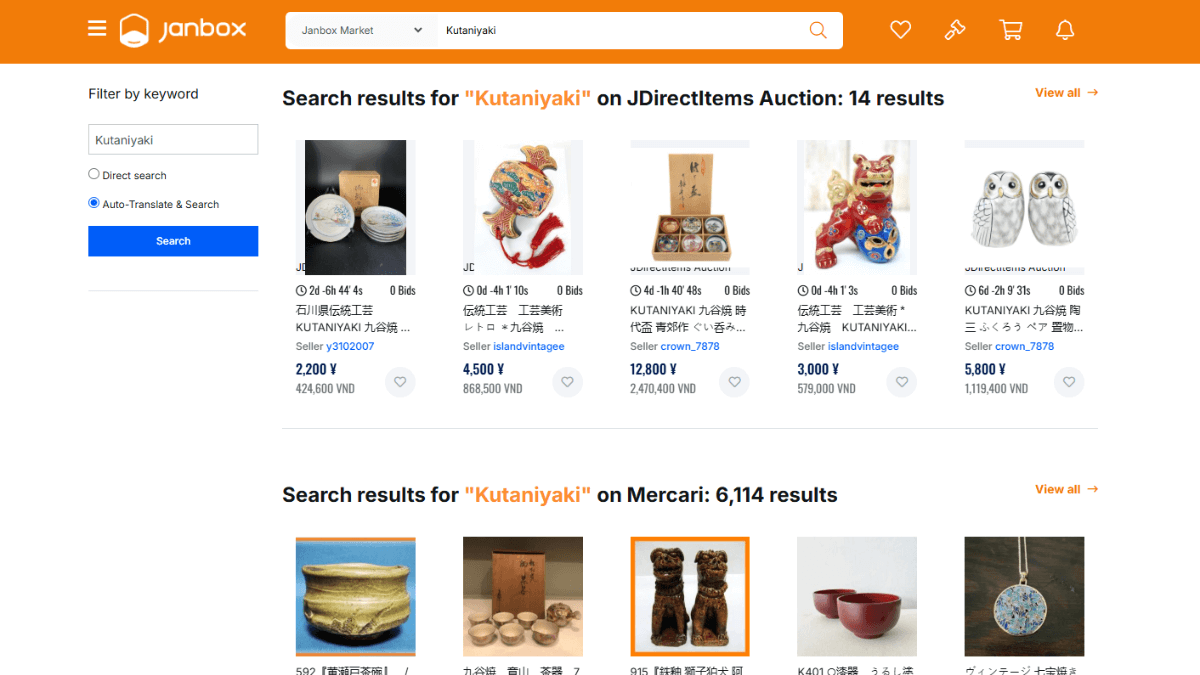
A pro tip: always check for artisan signatures or kiln marks to verify authenticity, as these distinguish true Kutaniyaki from imitations. Whether you’re a collector or gifting a loved one, these platforms make it easy to own a piece of Japan’s porcelain legacy with confidence.
>>> Read more: Top 20+ Best Things To Buy In Japan 2022 [Unique From Japan]
11. Conclusion
The height of Japanese colorful porcelain is thought to be Kutani-yaki ware. The complex patterns of Kutaniyaki are its distinguishing features. The vibrant overglaze decorations are almost works of art in and of themselves because they are lively but graceful. Have fun discovering the various painting techniques that have evolved over time. Visit the places listed below if you’re planning a trip to Ishikawa Prefecture to discover more about one of Japan’s greatest displays of handmade crafts.
- Website: https://janbox.com
- Email: [email protected]