As varied and distinctive as the anime figures themselves are the reasons behind collecting them. It’s a popular technique for people to fill their actual spaces with their favorite figures. For others, it’s a competition to amass a collection that can equal that of even the most seasoned collectors. It’s a common question among collectors: How are anime figures made? The following article will share more about interesting objects.
What are anime figures made of?
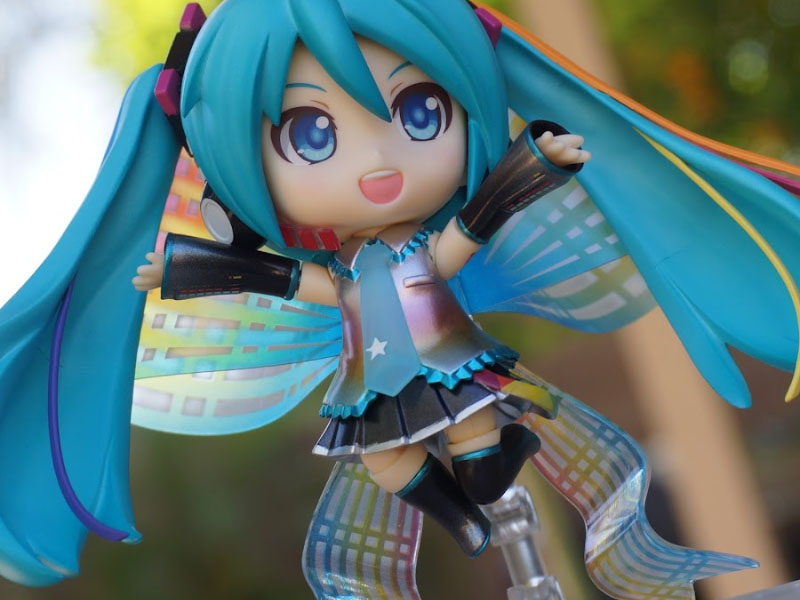
The prototype is made out of aluminum wire, modeling clay, and other sculpting tools. A plastic resin, such as acrylonitrile butadiene styrene, is used to create the real figurine (ABS). This is a tougher plastic that is utilized to create the main body. Smaller accessories and costume elements are frequently molded from softer polymers like polypropylene and polyethylene.
Bodysuits, capes, and face masks can all be made from a variety of textiles, including rayon and nylon. As a final touch, acrylic paints in various colors can be used to embellish the figurine as a final touch. Furthermore, more complex toys may include small electronic components that provide light and sound effects.
>>> Read more: How much anime figures cost in Japan | 3 tips to save money
How are anime figures made?
The Production Procedure
– Making the mold
The final clay prototype is used to create a master mold or a succession of molds. These molds are used to mass-produce the figure’s completed pieces. The fabrication and operation of the molds take up around two-thirds of the time it takes to create one action figure. For each item, patterns based on the prototype are created and sent out for assembly line manufacturing. Because manufacturing sites are often situated overseas, such as in Asia, this stage may take many months.
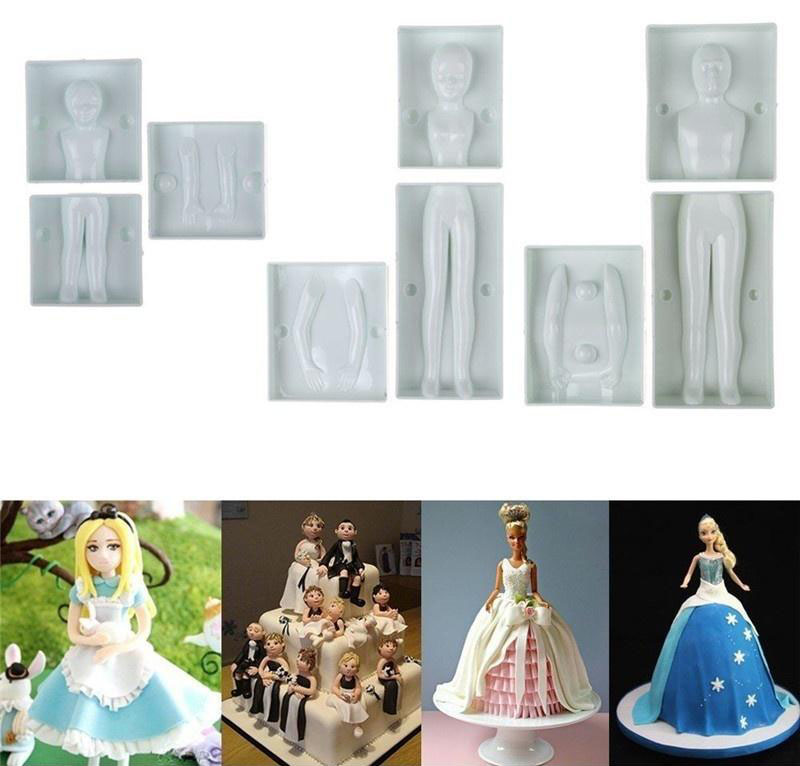
The designers must figure out how to turn the three-dimensional figure into a collection of plastic bits in the most efficient way possible. Some figurines are made of a single piece of plastic with a wire skeleton that allows for minimal mobility. Each moveable portion is sculpted as a separate component for figures with more articulation.
The Star Wars Storm Trooper toys, for example, have a hollow torso with solid vinyl limbs. Swivel joints are used throughout the figure to let the limbs move. Instead of a wire frame, this sort of figure has tiny gears and washers in the joints of the arms and legs, allowing the figure to bend to any angle and maintain that stance.
– Parts molding
The parts can be made using a variety of molding procedures. Hasbro, for example, explored using a rotational molding method to give their Star Wars figurines a smooth, seamless appearance. However, because of the size of the pieces, significant detail was lost, and this method was undesirable.
Another issue with rotational molding is that it is a slower process that costs the company more money. Hasbro chose to employ injection molding technology instead. Molten plastic is injected into a two-piece mold in this procedure. While the plastic cools and solidifies, pressure is used to keep the mold together. After that, the mold is opened, and the plastic part is expelled.
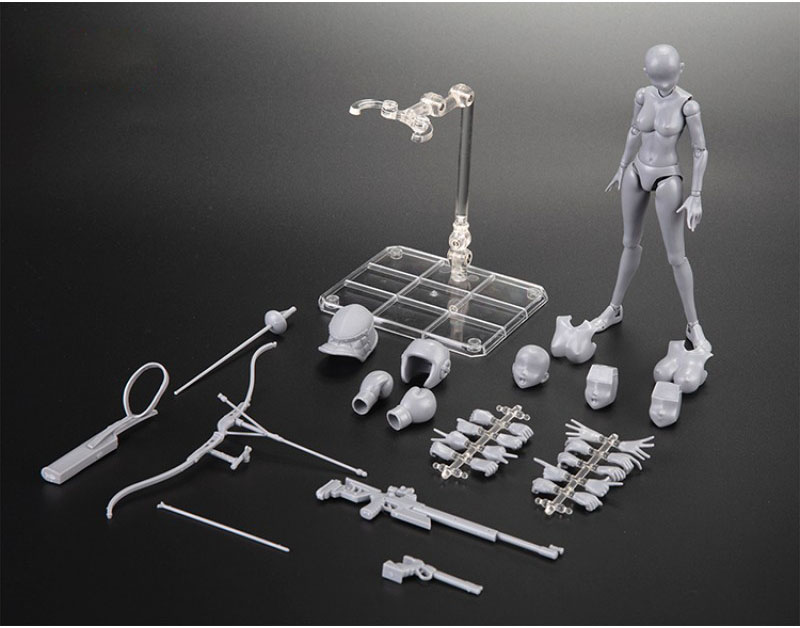
– Assembly
After all of the separate plastic, components have been made, the completed figurines are assembled. Some components may be linked together without the need for glue using an ultrasonic sealing process, which employs high-frequency vibrations to fuse the plastic. This method creates a more secure bond between the parts as well as a very thin, nearly imperceptible seam.
This method is used by Hasbro to produce figurines with a high degree of detail while maintaining production speed. Some supplementary elements, such as chest plates and boots, are attached with glue.
– Packaging and shipping
The packaging for the figure is being designed at the same time as the figure itself. A box with a transparent plastic window or a cardboard backing covered in a plastic blister should be common components of the packaging. Well-designed box images may increase the value of a figure, and some collectors never open figurines they buy to keep the artwork in immaculate condition.
Following the completion of the packaging design, it is mass-produced and shipped to the factory where the figurines are created. The figures are placed into the packaging, which is then sealed with glue or tape. The completed pieces are put into shipping cases and shipped to the United States by sea. The toys are then delivered to a variety of stores.
>>> Read more: What is Figma Figure Anime? The difference from other figures
The Design Process
The real design process begins with drawings of the prospective figure once the character has been chosen. The development of a clay prototype is the next phase. The backbone of the figure, called an armature, is created by bending metal wires. The wire shape incorporates the contour of the figure’s arms and legs into the overall position it will take. The sculptor then applies clay to the armature to get the correct weight and form. To solidify the clay, it may be baked briefly during the prototyping process. The sculptor then carves the clay with various tools, such as a wire loop, and shapes the figure’s features.
The sculptor may choose to withdraw the arms after developing the basic form and work on them independently for subsequent attachment. This provides the sculptor more control and allows him to work on the prototype with finer details. The sculptor molds the body with rough tools to get the appropriate level of detail. Photo and drawing references are employed to ensure the figure is as accurate as feasible during this step. Human models may even be used by certain sculptors to aid their design work.
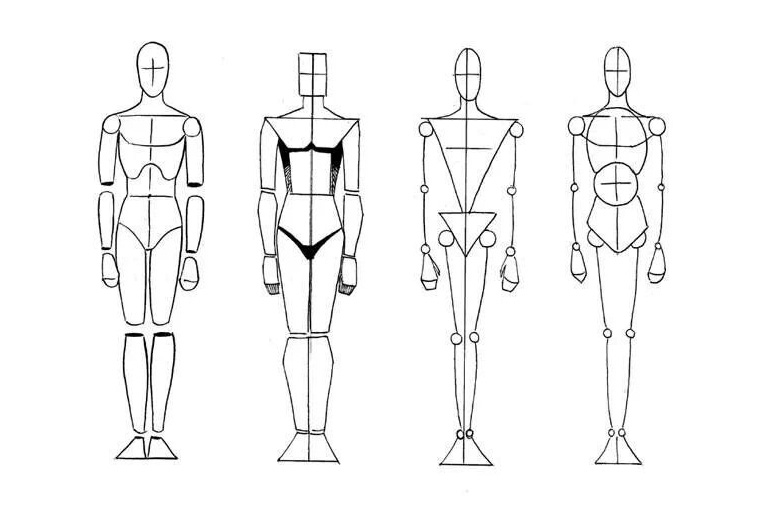
The sculptor adds the finer features once the overall body shape is complete, giving special attention to the eyes, nose, and mouth, which give the figure its lifelike look. While the true head is sculpted on a separate armature, the designer may attach a rough lump of clay to the main figure as a temporary head. This allows the sculptor to complete the figure’s facial expressions without having to worry about the rest of the body. The completed head may now be affixed to the main armature and bonded to the body with more clay. The neck and hair are molded to suit the figure appropriately when the head is fitted.
The outfit may then be molded directly onto the body, depending on the figure’s design. If a fabric outfit or uniform is to be added later, the prototype is sculpted without any specifics for the costume. Parts of the clay may be covered with aluminum foil during this procedure to prevent it from drying out too quickly. The entire figure is baked to solidify the clay after everything is finished.
The sculpted prototype is subsequently forwarded to the manufacturer for approval. Once all the design components are finished, the prototype is utilized to make the molds that will form the plastic parts for the mass-produced figure. The complete sculpting procedure might take up to two weeks, depending on the sculptor’s talent and pace. If the figure has to be revised, this process can be performed numerous times. This design phase is usually granted for many months.
>> Read more: Collect: 10+ Most Expensive Dragon Ball Figures.
The Quality Control
Action figurines for toys are manufactured under strict quality controls. Samples are sent back to the manufacturer for approval as the molds are made and tested at the manufacturing facilities. The figurines must next pass a number of rigorous safety and quality tests to guarantee that they are safe for young children and won’t break while being played with. It takes a month or two to stress test the packaging and repeatedly test the articulation of each figure. Where they actually ship a toy in its box, transit testing is used. To simulate the harsh treatment the box would experience before it is placed on the store shelf, further testing entails dropping and bouncing the container on the ground.
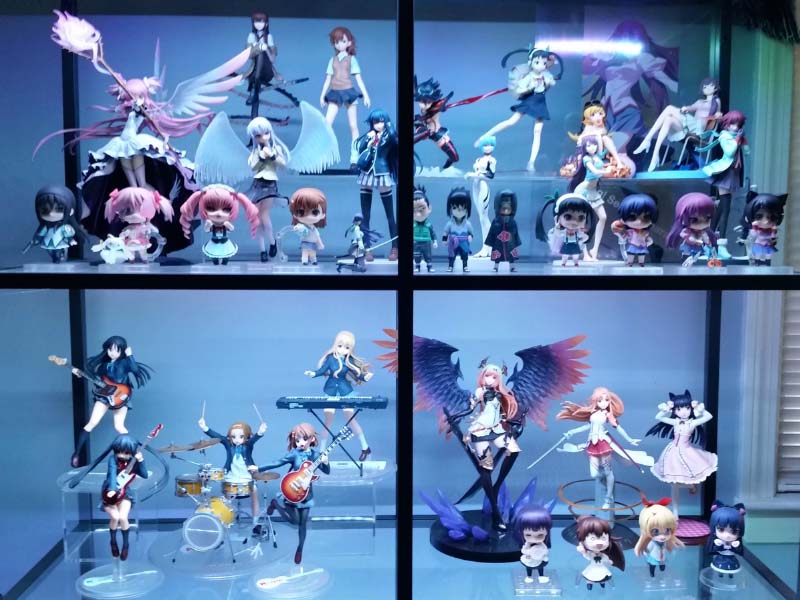
What is the best place to buy anime figures?
Unreliable dealers take advantage of the fact that it can be difficult to distinguish between genuine and fraudulent anime figures. On the internet, you may acquire fake anime sculptures, which may ruin your shopping experience. Why chance it by purchasing anime figures from shady websites? You should stick with well-known anime figurine sellers that have a ton of positive feedback.
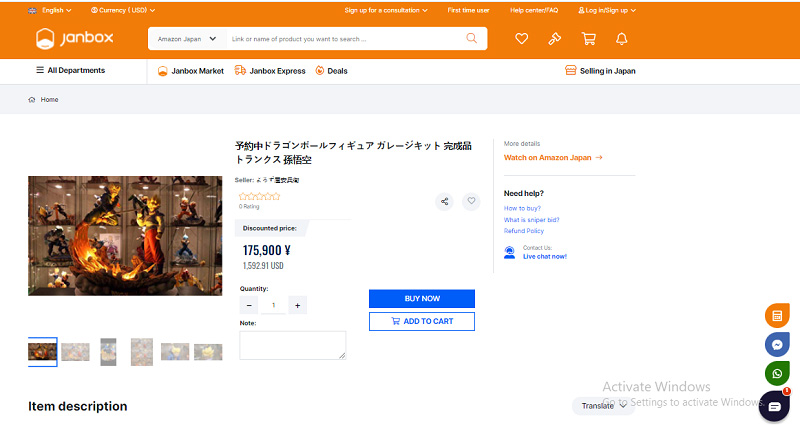
Janbox is an excellent option if you’re seeking the top websites to purchase genuine popular anime figures. As a legitimate proxy buyer, Janbox is associated with several sites that offer many types of anime figures for sale. You may be confident that you’ll always get genuine figurines from them because they are all respectable and well-trusted among anime enthusiasts.
>>> Read more: Top 18 Best Websites To Buy Anime Figures From Japan
Conclusion
Hobbies are often expensive, especially as you delve further into them. Purchasing an anime character might be an investment if you ever plan to sell them. Many individuals labor to make beautiful art pieces for fans to collect and possess. Each of them deserves to be acknowledged and rewarded. We hope that our answer to the question: “How are anime figures made?” will make you satisfy and maintain your interest in anime figures.
- Website: https://janbox.com.
- Email: [email protected].
- Facebook: https://www.facebook.com/janbox.com.en.